Validation Steps, Validation Model
Validation of equipment, facilities, and utility systems stands as a cornerstone in ensuring the quality, dependability, efficacy, and regulatory compliance of manufacturing equipment, facilities, software applications, and utility systems within pharmaceutical manufacturing and medical device production. It encompasses a series of meticulously executed activities and stages designed to achieve and maintain a validated state.
The V-model, alternatively known as the Verification and Validation model, offers a structured approach utilized across pharmaceuticals, medical devices, and engineering disciplines. This model ensures systematic and comprehensive design, development, and testing of systems. Its graphical representation resembles the letter "V", with the left side representing developmental stages and specifications resulting from development, and the right side mirroring corresponding testing and validation phases.
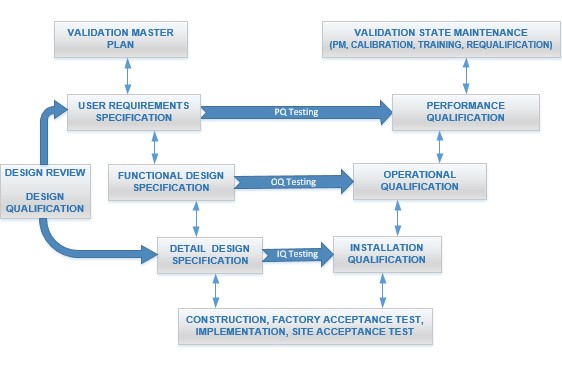
User Requirements Specification (URS) Phase
In the User Requirements Specification (URS) phase, the focus lies on gathering and documenting the requirements articulated by end-users or stakeholders. These requirements typically provide a high-level overview of what the system should achieve, prioritizing functionality over specific implementation details. The URS serves as the cornerstone for subsequent stages of development, guiding the creation of functional and detailed design specifications.
Functional Design Specification (FDS) Phase
Following the URS, the Functional Design Specification (FDS) is developed based on the gathered user requirements. This document delves into how the system will fulfill the specified requirements in terms of its functions, features, and overall architecture. It outlines the major components and interfaces of the system, providing a comprehensive framework for its development.
Detailed Design Specification (DDS) Phase
In the Detailed Design Specification (DDS) phase, the functional design is further refined into detailed specifications by engineers and designers. This involves creating intricate schematics, diagrams, and documents that specify how each component of the system will be implemented. The DDS essentially serves as the blueprint for the actual implementation of the system, ensuring alignment with the previously defined functional requirements.
Design Qualification (DQ) Phase
Design Qualification (DQ) follows, which is the process of verifying that the system's design meets the requirements specified in the URS. This phase involves meticulous review and approval of the documents and designs generated in the earlier stages. The primary objective is to ensure the completeness, accuracy, and feasibility of the design before proceeding to implementation.
Installation Qualification (IQ) Phase
Once the design is approved, attention shifts to the Installation Qualification (IQ) phase, which verifies that the system is installed correctly according to both manufacturer specifications and industry standards. This may encompass physical installation, configuration, and initial testing to ascertain that the system is properly set up and ready for use. IQ also involves confirming that necessary documentation, such as as-built drawings, equipment manuals, and supplier certificates, are in place.
Operational Qualification (OQ) Phase
Operational Qualification (OQ) focuses on testing the operational aspects of the system, ensuring that it functions as intended under normal operating conditions. Through a series of tests and procedures, this phase verifies that the system meets all functional requirements and operates reliably in its intended environment. This typically includes conducting performance tests, calibration verifications, and functionality checks. OQ also involves setting acceptance criteria and documenting the results to ensure that the system meets the predefined specifications and regulatory requirements.
Performance Qualification (PQ) Phase
Performance Qualification (PQ) serves as the final stage of validation, aiming to demonstrate that the system consistently performs according to predefined criteria. This involves executing a variety of tests and simulations to evaluate the system's performance under diverse conditions, ensuring it meets the needs of end-users and operates effectively in its intended environment. PQ may involve running the system for an extended period to assess its performance, reliability, and stability.